The Impact of Air Leaks on Energy Costs in Compressed Air Systems
Compressed air systems are widely used in industrial facilities and hold significant importance in terms of energy consumption. However, air leaks in these systems are a major issue that not only reduces energy efficiency but also increases costs. In this article, we will address the energy losses caused by air leaks and how these losses can be prevented.
What Are Air Leaks?
Air leaks are unwanted air losses in compressed air systems caused by sealing problems, which reduce system efficiency. These leaks are often not visible, like oil leaks, and are usually undetectable to the human ear. Nonetheless, air leaks are one of the primary causes of energy consumption in compressed air systems.
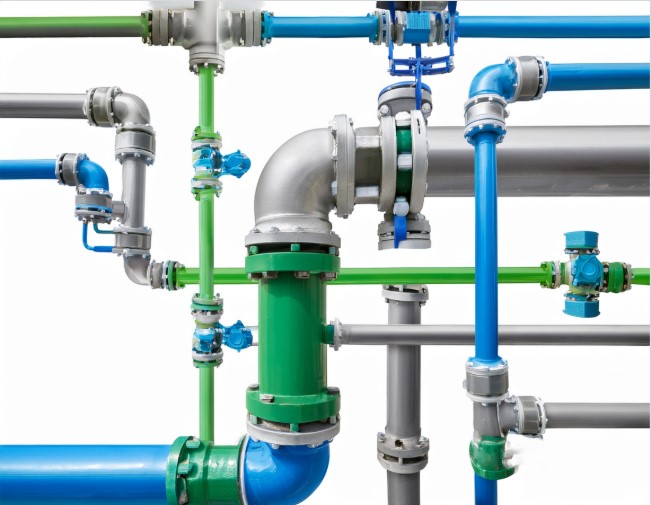
Where Do Air Leaks Occur?
Air leaks can occur at various points in compressed air systems. The most common leak points include:
- Couplings
- Valves and flanges
- FRLs (Filters, Regulators, and Lubricators)
- Drain valves
- Hoses, pipes, and connection points
- Leaks at these points reduce system pressure, increase energy consumption, and shorten the lifespan of equipment.
What Are the Effects of Air Leaks?
Air leaks cause several negative effects in compressed air systems:
Decreased System Efficiency: Leaks create pressure imbalances, reducing overall system efficiency.
Increased Energy Costs: Compressors must work harder to compensate for leaks, leading to higher energy consumption.
Reduced Equipment Lifespan: Leaks place additional strain on compressors and other equipment, shortening their lifespan and increasing maintenance costs.
How Are Air Leaks Detected?
Various methods can be used to detect air leaks:
Soap Bubble Test: Applying soap solution to suspected leak points can help identify air leaks. However, this method is time-consuming.
Ultrasonic Acoustic Detectors: Leaks generate ultrasonic sounds that can be detected with specialized devices. This method is particularly effective in noisy environments.
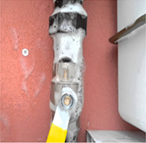
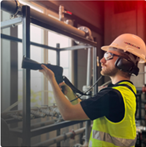
The Hidden Cost of Air Leaks
Air leaks significantly increase energy costs. For example, in a facility operating 8,000 hours per year, a 3 mm leak at 7 bar pressure can result in approximately 160,360 units of annual energy cost. Moreover, this cost is not limited to energy use alone. When equipment and maintenance expenses are included, the total cost can reach 208,260 units.
Savings Achieved by Eliminating Air Leaks
Eliminating air leaks can yield substantial energy savings. For instance, in a factory with a 160 kW inverter-driven compressor operating at an average load of 75%, the average power consumption is 130 kWh. Reducing compressed air leaks by 25% in such a facility can result in annual savings of approximately 1,040,000 units. Additionally, this saving is not limited to energy costs; it also extends equipment lifespan and reduces maintenance expenses.
ConclusionAir eaks in compressed air systems are a significant issue that lowers energy efficiency and increases costs. However, with regular leak detection efforts and preventive maintenance, these leaks can be minimized, leading to considerable energy savings. Preventing air leaks not only reduces energy costs but also extends equipment lifespan, thereby enhancing overall operational efficiency.